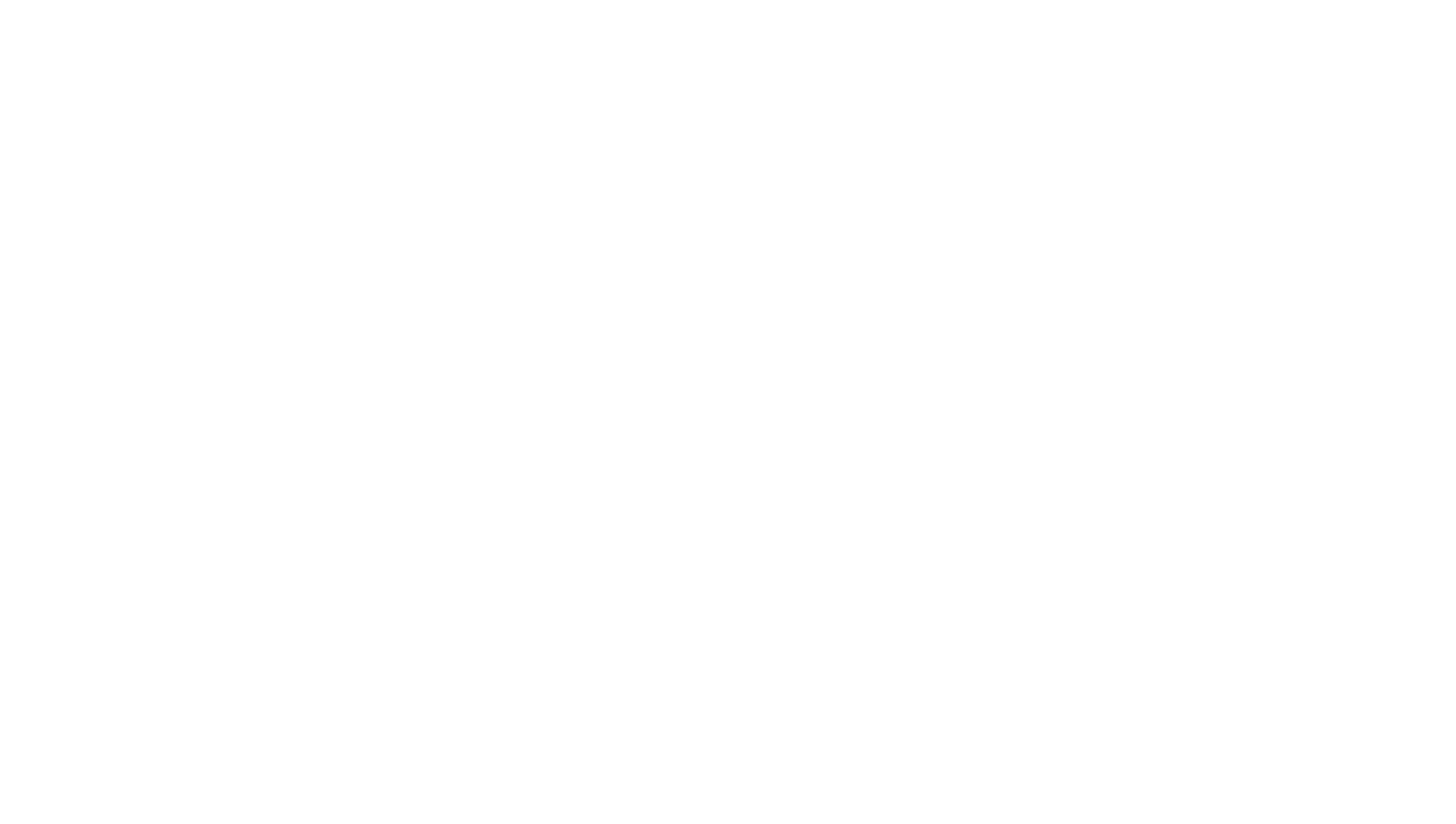


Source custom consumer electronics parts
-
From prototyping to production
-
Huge selection of high-quality materials & finishes
-
Get full IP protection and quality documentation




Electronics manufacturing for faster innovation
Hitting innovation deadlines and making it to market are crucial in the consumer electronics market. Protolabs Network speeds up the prototyping process and gets you to the production scale faster. We provide expert design support and can make exceptional parts with incredible cosmetic quality. With our instant quoting system and supplier network, you can bolster your supply chains and get custom parts for every prototyping, production and assembly need.

Protolabs Network is ISO 9001 certified and our suppliers have industrial certifications.
-
ISO 9001
-
ISO 14001
-
ISO 13458
-
ISO TS16949
-
AS 9100

Get validation reports to ensure the highest quality and compliance.
-
CMM Inspection Report
-
Full Dimensional Inspections
-
Material Test Reports
-
Material Certificates
-
Certificates of Conformance
-
First Article Inspections

We use a rigorous set of protocols and procedures to maintain quality.
-
Special tooling
-
Dimensional checks with calibrated equipment
-
Review of all quality documentation and industry certifications
-
Full IP protections on the platform and within the network
Parts in 1 day with Protolabs
Protolabs and its network work together to bring you the world's most comprehensive manufacturing solution. While the network can provide a large breadth of capabilities, Protolabs’ factories offer expedited manufacturing with automated in-house machines for the industry's fastest lead times.
Get quick-turn parts with Protolabs
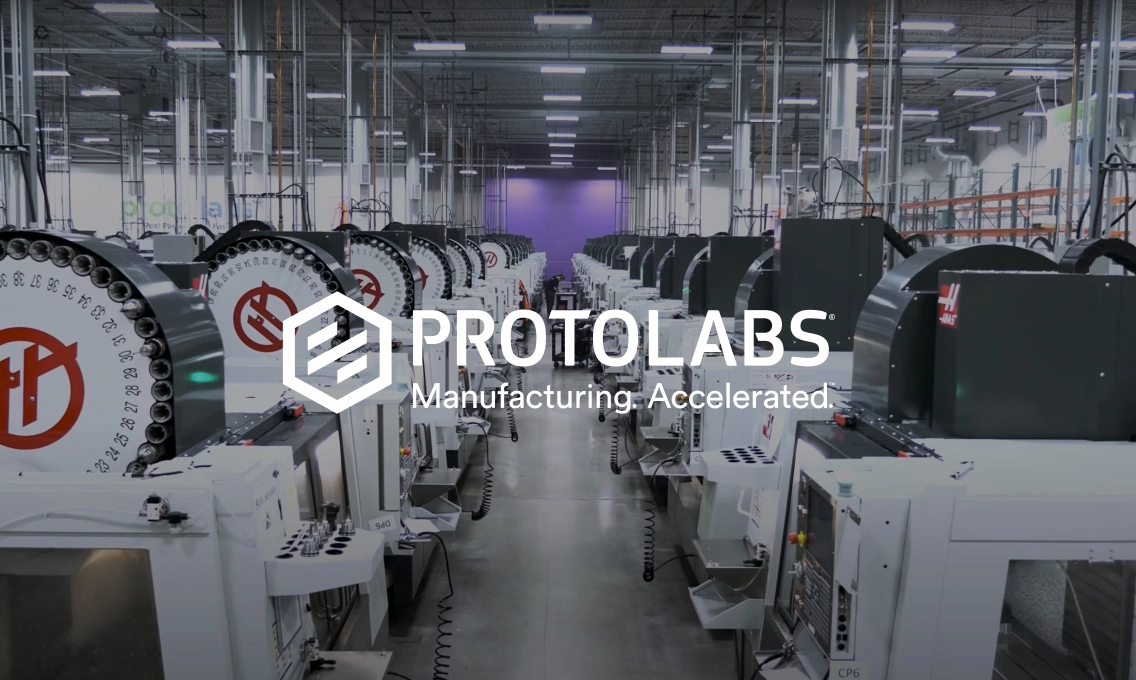
Manufacture appliance parts, electronics, consumer products & more with Protolabs Network










Manufacturing capabilities for consumer electronics makers

Milling, turning and post-processing
-
Tolerances down to ±.0008 in (0.020 mm)
-
Lead times from 5 business days

FDM, SLA, SLS, MJF
-
± 0.3% with a lower limit of ± 0.3 mm (± 0.012 in)
-
Lead times from 1 business day

Laser cutting, bending, post-processing
-
Tolerances down to ±.004 in (0.1 mm)
-
Lead times from 5 business days

Prototypes and production tooling
-
Wide range of part complexities and sizes
-
1 to 1M parts
Why major consumer electronics brands use Protolabs Network
Wonderffle
“As well as reducing my prototyping costs, Protolabs Network also serves as the team of developers and mechanical engineers you need to bring a product to market.”
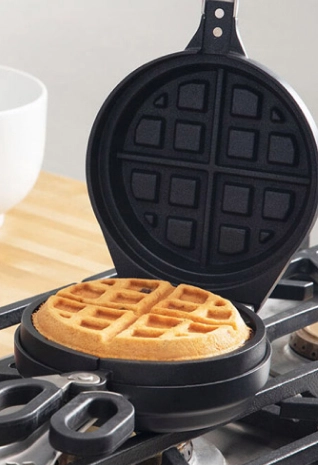
Materials & surface finishes for consumer electronics parts
Our vetted network of specialized manufacturing partners gives us access to a broad range of materials and surface finishing options for prototyping through to full-scale production.

Select from a broad range of durable & pristine materials
Aluminum:
5052,
6061-T6,
7075-T6,
2024-T351
Copper:
Copper C110,
Copper C101
Thermoplastics:
Polycarbonate (PC),
Polyoxymethylene (POM),
PEEK,
ABS
Commodity polymers:
Polypropylene(PP),
PVC,
Polyethylene (PE)
Composites:
Garolite G-10,
FR4

Select from these finishes to protect your parts
Anodizing
Powder coating
Electroless nickel plating
Insert installation
Heat treatment
Passivization
Gallery of consumer electronics parts
3D printing game-changing, customized mice and other devices
Formify is a startup with a mission to make it easier to access completely customized computer devices.
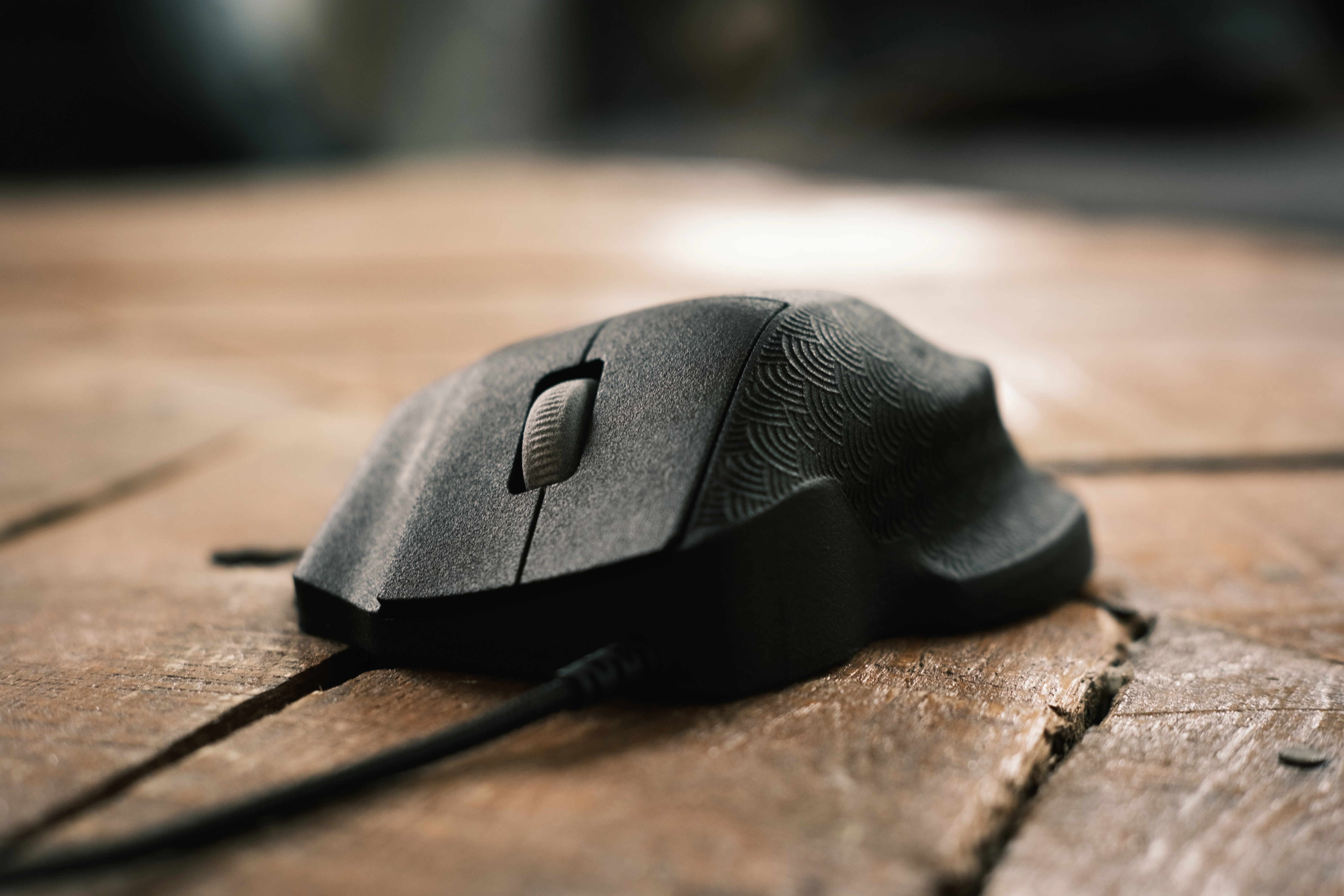
How Protolabs Network helps consumer electronics companies innovate
The Protolabs Network platform is the easiest way to get competitive pricing for comparing order volumes, lead times, materials, tolerances, secondary processes, and more for your projects. Get all final pricing information upfront, including shipping, quality control and customs clearance (when ordering from the US and EU). We prioritize IP protection on the platform and throughout the process to ensure that your designs and models are completely secure. Our platform is equipped with design for manufacturability (DFM) analysis and our mechanical engineers are always on hand to offer guidance to get the most out of Protolabs Network.
To keep your supply chain consistent and sturdy, we adhere to thorough quality control processes and protocols. Our manufacturing partners go through a complete vetting process before joining the network and on-site quality engineers perform frequent audits to ensure they meet the Protolabs Network Standard. Internal teams in Amsterdam and Chicago inspect parts for functionality and cosmetic specifications, and we handle all custom clearance requirements and ensure on-time delivery.
Thanks to our specialized network of cutting-edge manufacturers, we can offer customization options from single functional prototypes to higher volumes of parts that reach final customers. We have talented engineers in-house that can accelerate your innovation process and tweak designs to come off printers and machines looking and functioning better, even if every component is completely unique.
FAQ's
How do we ensure our manufacturing partners are ISO certified?
We do thorough checks of every manufacturing partner (MP) during the initial onboarding process and perform audits on processes and certifications every two years. To source parts from certified MPs, you can indicate these requirements on the platform or contact networksales@protolabs.com. We’ll match your designs with the right supplier.
How does Protolabs Network protect data and intellectual property?
Our platform is secure and encrypted to ensure that customer data and interactions with suppliers are all protected. All digital models and drawings are safely stored on AWS servers, located in Europe. MPs must sign our Manufacturing Partner Agreement as part of their onboarding, which contractually obligates them to keep customer data confidential. Our General Terms of Sale prohibit orders that misappropriate or infringe on copyrights, patents, design rights, trademarks, trade secrets and other IP rights.
What happens if a part doesn’t meet your specifications?
One of the reasons engineers use Protolabs Network is that we take on all the risks for you. If your parts aren’t up to spec, you can file a dispute claim and we’ll remake your components or refund your order. For more detail on how we handle disputes, you can contact our Customer Success Team. At the same time, we complete non-conformity reports for parts that don’t meet all requirements, with follow-up with manufacturers including root cause analysis and rapid corrective actions.
How do I request materials not listed on the site or platform?
If you want to get parts in specialized materials that aren’t listed on our site or platform, you can send a request to your account manager or contact networksales@protolabs.com. Our supplier network has access to a huge range of materials, so most of the time we are able to find a manufacturing partner to fulfill your request.
Put your consumer electronics parts into production today.
Get instant quote