The Protolabs Network Standard
Cosmetic standards
Finishes are differentiated into two categories, cosmetic and non-cosmetic. This is meant to standardise how good the finish should look, so that we can focus on doing only what your project really requires.
-
Cosmetic is the best option when visual consistency across batches is required and parts cannot have cosmetic defects on their "primary" side.
-
Non-cosmetic is the less expensive option. Parts can present slight visual differences and cosmetic surface imperfections.
When you select a cosmetic finish, we commit to producing high-end, customer facing products. We guarantee that you will receive "beautiful-looking" parts according to our cosmetic standards described below.
Visual inspection conditions
Surface quality on our side upon receiving will be visually inspected with the following conditions.
Distance | 50 cm +/- 10cm with a 10/10 vision (or corrected) |
Incidence angle | Approximately 45 degrees in all directions |
Lighting conditions | 500-1000 Lux, color 33000-5300 Kelvin (neutral white) |
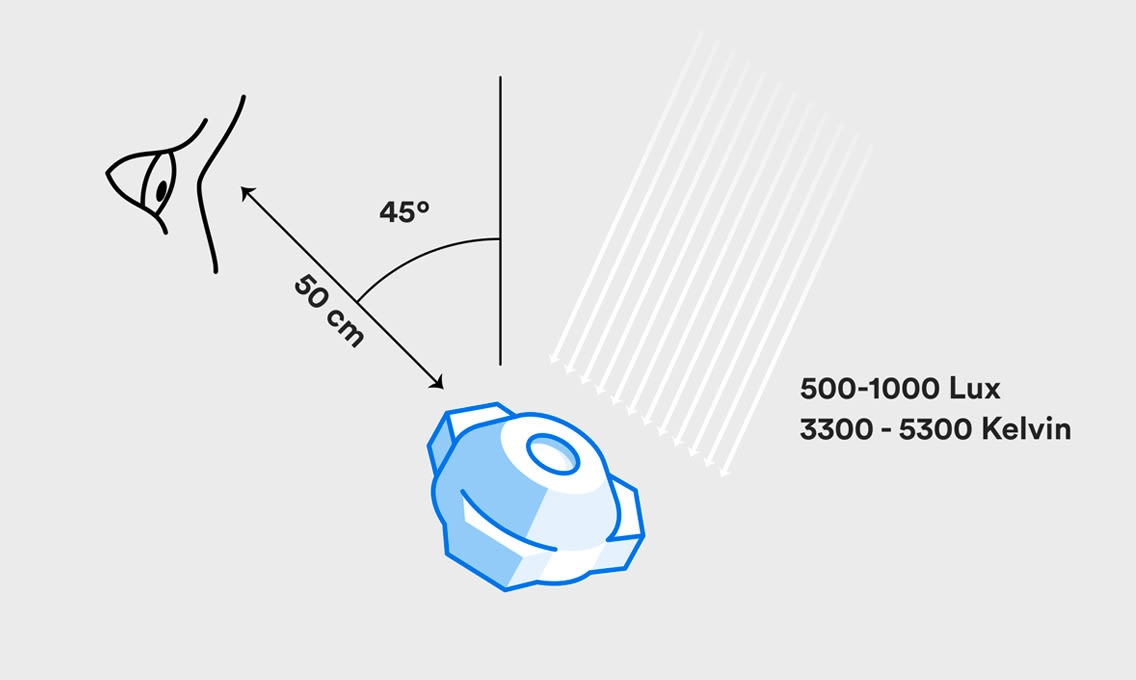
Quantification of cosmetic surface quality
The parts are guaranteed to be visually consistent across the same batch
-
Brush marks will be in the same direction
-
Same grit will be used across parts for sanding or brushing
-
Color will be consistent to the same hue when parts are placed next to each other
-
Gloss units will be consistent across the batch
Only minor defects are allowed on the hidden B side.
Defects | Primary side (A side) | Secondary side (B side) |
---|---|---|
Scratches, dents, stains, blemishes | None ** | None ** |
Hanging marks * | None ** | Minor hanging marks |
Minor defects | None ** | Up to two minor defects |
* When applicable to finish
** Not detectable under observation conditions. See next page for details
100% visual inspection will be conducted on all the parts/units
When required, primary (A) side and secondary (B) side need to be indicated on the technical drawing
Process requirement
1.Programming and process plan
Programming and process plan will be the same across the whole batch, unless adjustments needed for the quality result.
2. Raw material
Raw material will come from the same batch for the whole quantity of the parts, which is especially important for anodizing consistency output
3. Machining
Machining will be programmed so that minimal sanding is required to eliminates steps. Parts will not be stacked without protection to prevent dents.
4. Primary surface finish (brushing, blasting, etc)
Parts will be cleaned, degreased, and handled with gloves by the workers from that point, and never in contact with each other.
The primary finish will stay consistent across the batch: same grit of sandpaper, same direction, same process parameters for bead blasting.
5. Secondary surface finish (if applicable) (anodizing, painting, etc)
Finish will be done at the same factory, and in the same batch.
No re-anodizing is allowed on parts without permission. Batch should be the same (eg. anodizing).
6. Transportation, handling, packaging
Gloves are mandatory for handling, no fingerprints will be allowed, especially handling before anodizing. Packaging will be protective following our logistics standards, and individual packaging will preferred at the discretion of the supplier, to protect the sensitive nature of the parts.
Get your parts into production today
Get an instant quote